Single-Seat vs. Double-Seat Control Valves: Structure and Characteristics
On this page
Control valves are integral components in industrial automation systems, playing a crucial role in regulating fluid flow within various processes. Among the different types of control valves, single-seat and double-seat valves are widely used due to their distinct advantages and specific application scenarios. Understanding the structural differences and performance characteristics of these valves is essential for selecting the right valve for any given industrial application. This article provides a comprehensive overview of the structure and characteristics of single-seat control valves and double-seat control valves, highlighting their unique features, operational mechanisms, and suitability for different operational environments.
Single-Seat Control Valve
A single-seat control valve, also known as a straight-through single-seat valve, features a relatively simple structure comprising a valve body, valve plug, guide sleeve, bonnet, top cover, valve stem, and packing.
1. Structural Characteristics
Valve Plug and Seat: The single-seat control valve consists of one valve plug and one valve seat. The plug and seat are centrally aligned through the guide sleeve. Movement of the plug alters the flow area of the fluid, thus achieving flow regulation.
Top Cover and Packing: The top cover compresses the packing to prevent fluid leakage.
Valve Stem and Plug: The valve stem and plug are fixed together using connecting pins or interference fit pins.
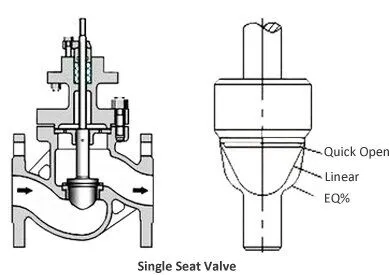
2. Operation
Direct-Acting and Reverse-Acting Valves: When the actuator moves linearly, it drives the valve plug through the stem. When the plug moves downward, the flow area decreases, known as a direct-acting valve; conversely, it is known as a reverse-acting valve. By reversing the connection position of the plug and stem, a direct-acting valve can be converted into a reverse-acting valve and vice versa.
3. Performance Characteristics
Low Leakage: Single-seat control valves achieve strict sealing and cut-off, using metal-to-metal hard seals or soft seals with materials like PTFE, with a standard leakage rate of 0.01% Cv (flow coefficient).
Limited Pressure Differential: For instance, the allowable pressure differential for a DN100 valve is only 120 kPa.
Small Flow Coefficient: The flow coefficient for a DN100 straight-through valve is only 100.
Unsuitable for High Pressure Differentials and Large Sizes: Due to the significant unbalanced force exerted by the fluid on the plug, single-seat valves are not suitable for high-pressure differential and large-size applications.
Plug Guiding Methods: Plug guiding typically employs top guiding. Some single-seat control valves use top and bottom guiding to enhance stability, while small flow globe valves often use seat guiding.
Double-Seat Control Valve
Double-seat control valves have a more complex structure, comprising two valve plugs and two valve seats, as well as a valve body, guide sleeve, bonnet, top cover, valve stem, and packing.
1. Structural Characteristics
Dual Plugs and Seats: The double-seat control valve features two valve plugs and two valve seats. Fluid enters from the left side, flows through both plugs and seats, and exits from the right side. The upward force on the upper plug and the downward force on the lower plug balance each other, resulting in minimal unbalanced force on the entire plug assembly.
Guiding Method: Double-seat control valves use top and bottom guiding to enhance stability.
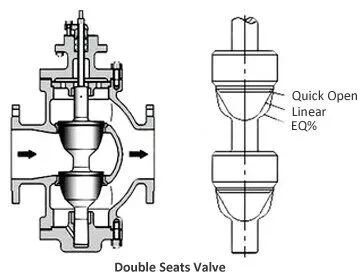
2. Operation
Conversion of Direct-Acting and Reverse-Acting Valves: By reversing the installation of the plugs and seats, a direct-acting valve can be converted into a reverse-acting valve and vice versa, without changing the actuator's action type.
3. Performance Characteristics
Minimal Unbalanced Force and High Allowable Pressure Differential: For example, a DN100 double-seat control valve can handle a pressure differential of 280 kPa.
Large Flow Coefficient: Double-seat control valves have a flow coefficient 20% to 50% higher than that of same-size single-seat valves. For instance, the flow coefficient of a DN100 double-seat valve can reach 160.
Higher Leakage: Due to the inability to simultaneously close both the upper and lower plugs, double-seat valves exhibit higher leakage rates. Variations in material thermal expansion can further increase leakage. However, recent designs have achieved leakage levels as low as class I to V with special integrated structures.
Poor Erosion Resistance: The complex internal flow path makes double-seat valves prone to severe erosion from high-pressure fluids, causing flashing and cavitation under high pressure differentials. This limits their suitability for high-pressure differential applications and control of fiber-laden and high-viscosity fluids.
Application Scenarios
Single-Seat Control Valves: Suitable for applications requiring strict sealing with low pressure differentials, such as precision control scenarios.
Double-Seat Control Valves: Ideal for high flow rate and high-pressure differential applications but with considerations for higher leakage rates and erosion resistance.
Single-seat and double-seat control valves each offer unique advantages and are suitable for different fluid control applications. Single-seat control valves, with their simple structure and excellent sealing, are ideal for low-pressure differential, small flow control. In contrast, double-seat control valves, with their ability to handle larger flow rates and higher pressure differentials, are better suited for demanding applications, albeit with higher leakage and erosion considerations. Selecting the appropriate control valve type involves balancing specific operational requirements and achieving optimal control performance and economic efficiency.